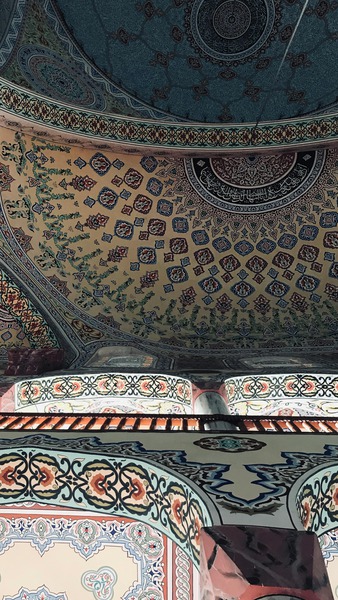
Ceiling tiles are a staple in modern architecture, providing both aesthetic value and functional benefits such as sound absorption and fire resistance. These tiles come in various materials, sizes, and patterns, but have you ever wondered how they are made? Let’s delve into the manufacturing process that transforms raw materials into the ceiling tiles we see in offices, homes, and other buildings.
The Base Material Selection
The journey of creating ceiling tiles begins with selecting the appropriate base material. This choice largely depends on the type of ceiling tile to be manufactured. Common base materials include:
-
Mineral wool, for its sound-absorbing properties
-
Fiberglass, for durability and acoustic performance
-
Metal, favored in commercial spaces for its modern look and fire resistance
Each material offers distinct advantages and is chosen based on the desired characteristics of the finished product.
Designing and Molding
Once the base material is selected, it is cut or molded into shape. For tiles intended to provide acoustic benefits, details such as the pattern of perforations or fissures are carefully planned. These design features are crucial for optimizing sound absorption and contribute to the overall aesthetic appeal of the tile.
Mixing and Wet Forming
Non-metallic tiles often proceed through a wet forming process. This involves:
-
Combining the base material with water and other additives
-
Forming a slurry that is then shaped into sheets or panels
-
Applying heat and pressure to solidify the shape, resulting in a robust tile
The specific recipe and forming technique are closely guarded secrets, tailored to produce tiles that meet strict industry standards.
Coating and Finishing
After the tiles are formed, they may receive a protective or decorative coating. This step is crucial for enhancing the functionality and longevity of the ceiling tile. Coatings can provide:
-
Moisture resistance
-
Increased reflectance for better light dispersion
-
Aesthetic finishes that mimic textures or patterns
The tiles are then left to cure, ensuring the coating adheres well and performs as expected.
Cutting to Size and Edge Detailing
The cured tiles are cut to standard sizes or custom dimensions as per requirements. Edge detailing is also performed, which caters to the installation system the tiles will fit into. Options for edge detailing include square, regular, and beveled edges, each offering a unique look once installed.
Quality Checks and Packaging
No tile leaves the manufacturing plant without undergoing rigorous quality checks. These inspections ensure that each tile meets specific criteria for:
-
Dimensional accuracy
-
Visual appeal and finish
-
Physical properties such as strength and fire resistance
Approved tiles are then packaged securely to prevent damage during transportation and storage.
Special Considerations for Acoustic Performance
For specialized applications, manufacturers focus heavily on the acoustic performance of ceiling tiles. When dealing with acoustic tiles ceiling installations, the production process includes designing the porous structure of the tiles to optimize noise reduction and create a more pleasant sound environment.
Customization for Specific Environments
Some spaces require unique solutions, like restaurant ceiling tiles, which may demand a balance between acoustics, aesthetics, and cleanliness. Manufacturers customize tiles to serve the specific needs of these environments, ensuring performance that supports a positive customer experience.
Technological Advancements
Innovation is a constant in the ceiling tile industry, with acoustical ceiling tile manufacturers incorporating new technologies to improve the sustainability and functionality of their products. Advancements in raw materials and the production process lead to higher-quality tiles that meet evolving architectural trends and standards.
Environmental Impact and Sustainability
The positive impact of these adaptations in manufacturing processes reverberates beyond environmental benefits. There is a growing demand in the construction industry for materials that are not only functional and aesthetically pleasing but also environmentally responsible. By committing to sustainable production methods, manufacturers of ceiling tiles can meet this market demand.
This integration of sustainability into product offerings can also offer a competitive edge as more builders and developers seek building materials that contribute to greener construction projects and certifications like LEED (Leadership in Energy and Environmental Design).
Key Contributions to Sustainability in Ceiling Tile Production
-
Incorporation of Recycled Materials: The use of recycled content in the production of new ceiling tiles significantly reduces the demand for new raw materials and helps to lower the industry’s carbon footprint. It also sets a precedent for the responsible use of resources in manufacturing processes.
-
Efficiency in Resource Use: Streamlining waste management and water usage in the manufacturing process illustrates an impactful approach to resource conservation. These efficiency improvements are crucial for sustainable production and for adhering to stricter environmental regulations.
-
Energy-Saving Manufacturing Processes: Employing energy-efficient techniques and technologies in ceiling tile production not only curtails energy consumption but can also result in cost savings over time. Sustainable energy practices contribute to the broader goals of decreasing industrial energy dependency and mitigating pollution.
As the intersection between environmental impact and industrial manufacturing becomes increasingly pronounced, the importance of sustainable production practices grows. The ceiling tile industry’s shift toward integrating recycled materials, reducing waste and water usage, and embracing energy-efficient processes showcases this commitment to sustainability.
More significantly, these changes demonstrate to consumers and investors alike that environmental responsibility and manufacturing success can go hand in hand, ensuring a better future for the planet and the economy.
Wrapping Up
The manufacturing process of ceiling tiles is a fusion of art and science. From the precise selection of base materials to the specialized requirements for sound absorption and environmental consciousness, each step is integral to the creation of the final product. Ceiling tiles may be overhead, but they’re hardly an afterthought in the realm of manufacturing excellence and interior design.